Development of a modular system for filtering toxic and flammable gases in conjunction with a suitable container for transporting damaged to non-transport-safe (critical) lithium-ion batteries
Dr. Ing. Ilian Dinkov (FFB), M. Sc. Jan Braun (FFB), M. Sc. Mona Meyer-Hollmann (LogBATT GmbH)
1. Presentation of cooperation partners KIT and LogBATT
The research project on which this report is based, the development of a modular filter system integrated into battery transport boxes, was carried out jointly by the cooperation partners of the Research Centre for Fire Protection Technology at the Karlsruhe Institute of Technology and LogBATT GmbH.
Founded in 1950 and affiliated to the Engler-Bunte Institute, Chair of Combustion Technology (EBI-VBT) of the University of Karlsruhe (KIT), the Research Centre for Fire Protection Technology is engaged in research and development work in the field of preventive and defensive fire protection.
The logistics company LogBATT GmbH, founded in 2017, specialises in the ADR-compliant transport of critically defective lithium-ion batteries and develops and produces its own safety containers, so-called SafetyBATTboxes for the storage and transport of lithium-ion batteries. Such safety containers must be officially certified by the Federal Institute for Materials Research and Testing (BAM).
Only if the following legal requirements are met during a real fire test, the containment will receive an official approval:
- Temperature of the outer surfaces of the complete package must not exceed 100°C. A short-term temperature peak of up to 200°C is permissible.
- No flame should be allowed to form outside the package.
- No projectiles may escape from the package.
- The structural integrity of the package must be maintained.
- The packaging must have a gas management system. This must be able to handle pressure surges and have HF management.
- The HF concentration in the filtered flue gas must be below the AEGL 2 limit value. These limit levels correspond to concentration guide values according to the Major Accidents Ordinance and are 12 ppm and 9.8 mg/m respectively.3
2. SafetyBATTboxes: new generation of safety containers for safe storage and hazard-free transport of lithium-ion batteries
Lithium-ion batteries can pose a wide variety of potential hazards:
- Thermal, chemical, electrical and kinetic
The SafetyBATTboxes have been designed with a wide range of safety measures to contain all the above-mentioned potential hazards from LIBs and to shield them from the outside. In the event of a battery reaction, the thermal event inside the SafetyBATTbox is contained and only the resulting flue gas is discharged to the outside via defined venting openings.
3. What happens in a battery fire
Rechargeable batteries are booming: they can be found in virtually all mobile consumer electronics devices, power tools, gardening tools, electric bicycles (pedelecs and e-bikes) and electric cars.
Since lithium-ion batteries are designed to provide a large amount of electrical energy, the chemical energy contained in these batteries is considerable. High-quality cells available on the market from well-known manufacturers contain several safety devices inside the cell that can “shut down” the cell as an electrical system in an emergency. However, if the lithium-ion batteries/modules/cells are misused, e.g. due to overcharging or discharging, overheating, mechanical damage or an internal cell defect, a thermal reaction, the so-called thermal runaway of the cell, can occur. If the thermal runaway of one or a few individual cells causes a thermal runaway of the entire system (module and/or battery), this is a so-called thermal propagation event. In a thermal runaway, an uncontrolled reaction occurs between the two electrodes and the stored chemical energy is released in one fell swoop. The dangerous thing about a thermal runaway is the combination of the materials used in lithium-ion batteries in conjunction with the high energy density mentioned. Due to the enormous heat development (sometimes > 1000°C on the surface of the cell), one or a few individual defective cell(s) is often enough to set the entire battery on fire. The danger of a thermal runaway is particularly present in accident-damaged batteries or batteries that are generally no longer safe to operate.
During this thermal run-through of the cell, the material contained in the cell decomposes and gas is produced. This creates an overpressure in the cell until it finally bursts open and the gas produced is blown off to the outside. This mostly white-greyish gas consists mainly of evaporated electrolyte, its reaction products and other cell components (for measured data, see chapter 4). This gas is highly flammable and can cause a so-called oxyhydrogen explosion, flash fire and fire.
4. Research project for the further development of the SafetyBATTbox filter system
In general, the containment vessels cannot completely absorb the very large quantities of gas that are released in the event of a thermal runaway and must therefore “blow off” (so-called vents). For example, approx. 44 l of flue gas can escape from a commercially available 18650 round cell. These emitted gases are both toxic and usually flammable, which is why they should be filtered before leaving the transport box and the gas outlet of the safety containers should also have a flame-retardant effect.
During the research project, basic investigations into filter effects, material tests and flue gas analyses were carried out, and research and tests were carried out on an advanced filter system as an integral part of a transport box.
The future filter system should fulfil the following tasks:
- The filter as a component of the gas management system is the only opening of the transport box to the outside. It prevents a critical overpressure from building up in the box.
- Preventing the spread of fire by preventing the flames from penetrating through (flame blocking effect).
- Insulation effect, filter system must compensate for or prevent heat penetration of the transport box via the venting surfaces.
- As extensive as possible retention/filtering of flammable and toxic substances from the escaping flue gas.
In order to gain basic knowledge about the composition of the escaping smoke gases, filtering possibilities, suitable materials, etc., battery fires were started in the SafetyBATTboxes and various measurements were carried out during this process.
First, analyses were carried out on unfiltered flue gas escaping from a lithium-ion battery fire and then various types of SafetyBATTboxes were set up with different filter systems and comparative measurements of the escaping flue gas were carried out on them.
For example, in the course of the research project, various filter systems were tested in so-called SafetyBATTboxes type M. For each of the fire tests, a lithium-ion cell module (12 kg, 2.14 kWh, prismatic cells, NMC cell chemistry) was (12 kg, 2.14 kWh, prismatic cells, NMC cell chemistry) was brought to thermal runaway by means of overheating (ceramic radiant heater).
The modules were each charged to approx. 100 % SoC before the start of the test. For the fire tests, the box was equipped with a variety of sensors and probes, including temperature sensors in and on the box, pressure sensors to measure the pressure difference between the inside of the box and the environment, and the pressure drop of the filter system. The outside temperature was continuously documented with a thermal imaging camera and the weight loss with a scale. The SafetyBATTboxes are double-walled and have an outlet on each side. Each of these is equipped with a flame arrester. The sampling probes for the emission measurement were positioned at the outlets of the SafetyBATTbox, in each case after the flame arrester. In addition, a sampling probe was placed in the box during the first test in order to obtain a zero measurement of the resulting flue gas. In addition to the usual flue gas components (O 2, CO, CO 2), the measurement also included a broad flue gas spectrum.
Figures 1, 2 and 3 show exemplary shots of the test preparation: Installation of the module in the SafetyBATTboxes (Fig. 1), incl. the packaging of the module using packaging material specially developed by LogBATT GmbH (Fig. 2). The lid of the SafetyBATTboxes has a seal and is fitted with tension locks all around. Figure 3 shows the closed box and the installation of the measuring instruments (exhaust gas probes, pressure sensors and thermocouples).

Figure 1: Cell module in the SafetyBATTbox

Figure 2: Packing material

Figure 3: SafetyBATTbox before the fire test incl. measuring instruments
Figure 4 shows an example of some sections of the real image and thermal image recordings during the thermal runaway test. The images in the same row were taken at the same time. It can be seen (see figure 4.1) that after a certain overheating time, the cells of the module, directly below the radiant heater, lead the thermal runaway into the corridors with a relatively moderate smoke development. Subsequently, the thermal event continues to propagate (thermal propagation) until the entire module has undergone thermal runaway. The thermal runaway in the box is characterised by a rather high temperature, as well as a high pressure rise. The images in Figures 4.3 to 4.6 show the discharge of the reaction products in the form of a massive emission of flue gas. After a short time, the reaction is finished, the amount of flue gas decreases noticeably and the module continues to smoke (see Fig. 4.7 and 4.8).
Figure 4: Real images and thermal images during and after thermal runaway and thermal propagation.
As mentioned above, the thermal run-through of a module in the SafetyBATTbox is associated with high temperature and pressure gradients. Figure 5 shows the temperature curves inside the box during the test. Directly above the module (T1-T3) the temperatures reach maximum values of about 800 °C. After leaving the box, the exhaust gases cool down to values below 250 °C (T5-T8). On the outside of the box, maximum temperatures of always below 80 °C were measured due to the double-walled construction. This means that the legal criteria regarding temperature are fulfilled.
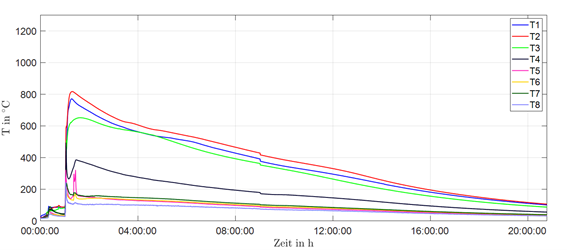
Figure 5Temperatures inside the SafetyBATTbox

Figure 6: Pressure difference
The measured pressure curve in figure 6 shows maximum values above 120 mbar. The figure also shows the thermal runaway of the individual cells (twelve individual cells in the module).
A comparison of selected pollutants, some of which are relevant for statutory approval
(HF emissions) with and without a filter system is shown in Table 1.
Fabric | Without filter system | With filter system | Adsorber effect |
Total carbon (C) | max. approx. 21,000 ppm | max. approx. 17,144 ppm | 18,3 % |
Hydrogen fluoride (HF) | 13 mg/m 3 | 0.9 mg/m 3 | 93 % |
Benzene | 261 mg/m 3 | 142 mg/m 3 | 45,6 % |
Dimethyl carbonate (DMC) | 13.475 mg/m 3 | 5,524 mg/m 3 | 59 % |
Ethyl methyl carbonate (EMC) | 7,411 mg/m 3 | 2,394 mg/m 3 | 67,7 % |
Main components deposits | Lead, chromium, | cobalt, copper, | manganese, nickel |
The new filter system has significantly higher filtering effects compared to measurements taken completely without a filter system. This means that the newly developed filter system, in addition to meeting the legal requirements for pollutant limits (HF < 9.8 mg/m 3), achieves an additional reduction of a wide variety of pollutants in the escaping flue gas. During the fire tests, the following substances were detected as main constituents in the flue gas in addition to the usual fire gases:
- Solvent vapours of the unburnt electrolyte and its reaction products
- Hydrocarbons as decomposition and reaction products of the organic solvents and the conducting salt, these include:
- short-chain alkanes, alkenes and alkynes (C1 – C10) such as methane, ethane, ethene, propane, propene etc.
- Carbon monoxide (CO) and dioxide (CO 2)
- Species containing fluorine and phosphorus (hydrogen fluoride (HF), hydrofluoric acid (HF (aq)), phosphoric acid (H 3PO 4), hydrogen phosphide compounds e.g. phosphine etc.)
- Hydrogen chloride
- Hydrogen (H 2)
- Nitrogen oxides such as nitrogen monoxide and dioxide (NO x, N 2O)
- Other hydrogen carbonates (benzoles etc.)
- Oxygen (O 2)
- Released conducting salt, e.g. lithium hexafluorophosphate (LiPF 6)
- Graphite dust
- Light and heavy metal particles such as aluminium, nickel, cobalt, copper, manganese, chromium, lead, lithium, etc.
- Other released particles and dusts (ash, soot, etc.)
Many of these substances have one or more of the following hazards: very toxic, harmful, carcinogenic, dangerous for the environment, irritant, flammable, corrosive, mutagenic, oxidising.
The results of the flue gas analysis show that a complete removal of all toxic, flammable or other hazardous components of the flue gas occurring in Li-ion battery fires is hardly technically feasible (under the given framework conditions). However, these can be greatly reduced by the filter system developed during the research project.
From all the investigations and analyses carried out, it can be deduced that a combination of different filter materials can have a positive effect on the filter effect. A mixture of different filter materials (also with regard to grain size and structure), each of which has a targeted effect on specific gases, is superior to a universal filter. To achieve the best possible filter effect, different materials should be combined in future filter systems.
The knowledge generated during the research project includes:
- Comparable gas analyses of different filter systems in real fire tests
- Analyses Pollutant loads Filter system and deposits
- Detection of main components of flue gas
- Detection Influences on flue gas composition
- Investigation and tests on various possible filter methods and different filter materials
- Development of a modular filter system, accordingly scalable filter systems for different sizes of transport containers possible
In summary, LogBATT GmbH, together with the Research Centre for Fire Protection Technology at KIT, was able to create a solid basis with regard to flue gas filtration of lithium-ion battery systems and is ready for future filter requirements in transport boxes for lithium-ion batteries. This is because the SafetyBATTboxes, with the newly developed filter system in the course of the research project, achieve an average reduction of more than 55% in the emission of pollutants in the flue gas during a lithium-ion battery fire.